Our Technology
- Home
- Our Technology
Institutional Video
OUR DECARBONIZATION SOLUTIONS
The Tecnored process is an innovative technology, with more than 100 registered patents in 38 countries. The Tecnored technology produces similar quality pig iron to the blast furnace in a comparable fashion, by feeding fuel (coal or carbon) and iron ore agglomerates into a furnace, together with hot air fed through tuyeres.
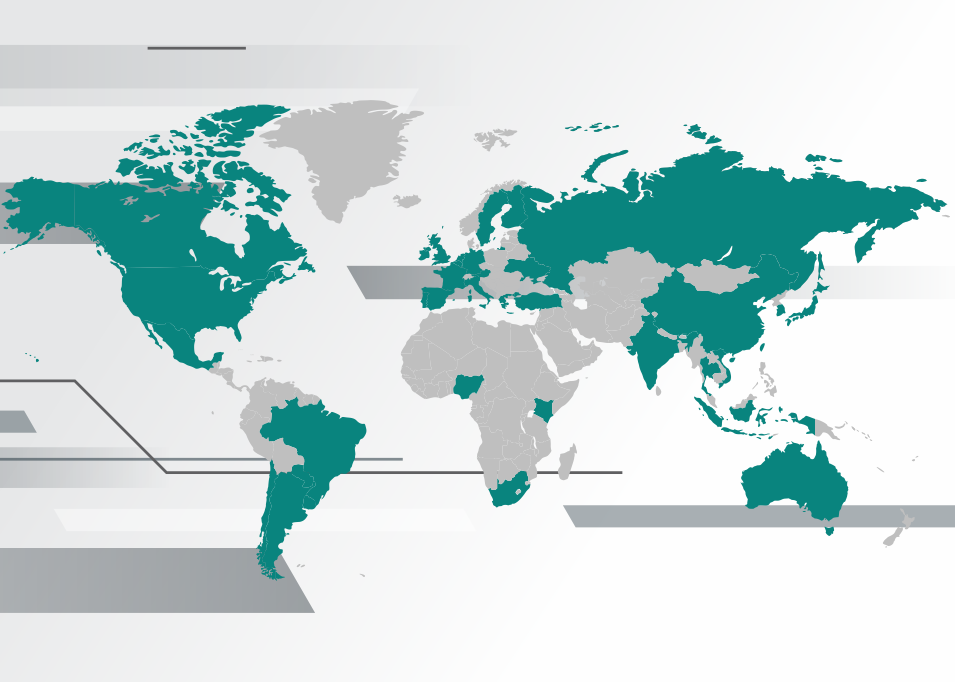
Tecnored Briquette – we are prepared to decarbonize steel production immediately
Cold-briquetting provides great flexibility
The cold briquetting process is different in several important ways for traditional sintering and coke-making.
1. It is a simple, flexible, highly controllable and repeatable process whereby the raw materials are precisely measured on feeding into the intensive mixer prior to briquetting.
2. The product is uniform and can easily be sampled and tested to ensure quality control
3. It can be easily and precisely reproduced at laboratory scale
4. It uses small and low cost equipment
5. It is easy to automate
Low cost Fuel briquettes are the key to competitiveness and low CO₂ emissions
Experience has shown that the higher density of briquettes compared to coke off-sets the higher ash content, leading to a greater thermal contribution and consequently higher pig iron temperatures.
The development of the fuel briquettes has been continuous since the commissioning of the plant in 2011. In the early campaigns Tecnored used coke as fuel, whilst the basic process control of the furnace was mastered.
The economic viability of Tecnored was fully demonstrated in 2018 when the furnace was operated stably and consistently using 100% fuel briquettes with thermal coal with a high ash composition. The use of cheap and abundant thermal coal and co-generating power from the furnace off-gases means that unit consumption of coal does not have a significant impact on plant economics.
It is this flexibility in the briquetting of fuel that is also the key to low CO₂ emissions, as it allows bio-char fines to be used. As a car reduces net emissions by burning alcohol produced from sugar-cane, so Tecnored reduces net CO₂ emissions by using bio-char produced from similar energy-cane crops.
In addition to dedicated highly productive grasses, developed specifically as energy crops, a wide range of agricultural waste streams from both food and forestry crops can be charred for use.
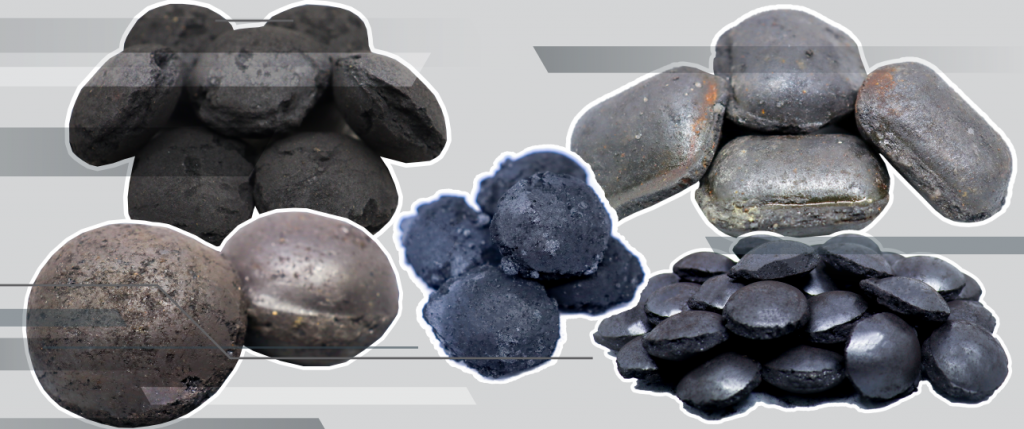
Sources of iron units
The reactor geometry was designed and has been modified to have ample flexibility in the use of raw materials, and many have been tested, such as standard iron ore pellet feeds, mill scale, nickel ores as well as dust and sludges generated in the steelmaking process.
The principal restriction of the source of iron units is the granulometry required to produce high quality briquettes. In general, the materials are fine with more than 50% passing 0.1 mm. Several standard iron ores have been used without process limitations.
As there is a ready supply of mill scale available at no cost at the São Paulo plant much of the operation has been carried out with this material, proving the ability of the process to effectively use this material which is troublesome in many steel producing regions. Mill scale has an advantage of being a high grade iron source, with the majority of the oxide is in the form of wustite (FeO).
Carbon sources used as Reductant
Similar to the metal units and fuel used in Tecnored a wide range of reductants has been used, ranging from bio-char, anthracite, petroleum coke to low cost thermal coals.
Once again, as there is a ready supply local to the industrial plant of low cost blast furnace dust (residue from blast furnace gas cleaning systems) this material is regularly used, in addition to the other Carbon sources.
Both mill scale and blast furnace dust show high chemical and size variability. The flexibility inherent in the briquetting process allow for continuous and automated adjustments in raw material, additive and water dosage, depending on the feed raw material variations measured. As such the Tecnored process was kept fully stable despite the use of these residues of varying quality.
The Tecnored process has been developed and refined at an industrial plant in São Paulo, Brazil, with a capacity of between 50-75 kta depending on the raw materials used. Since it was commissioned in 2011 it has operated with a wide variety of raw materials.
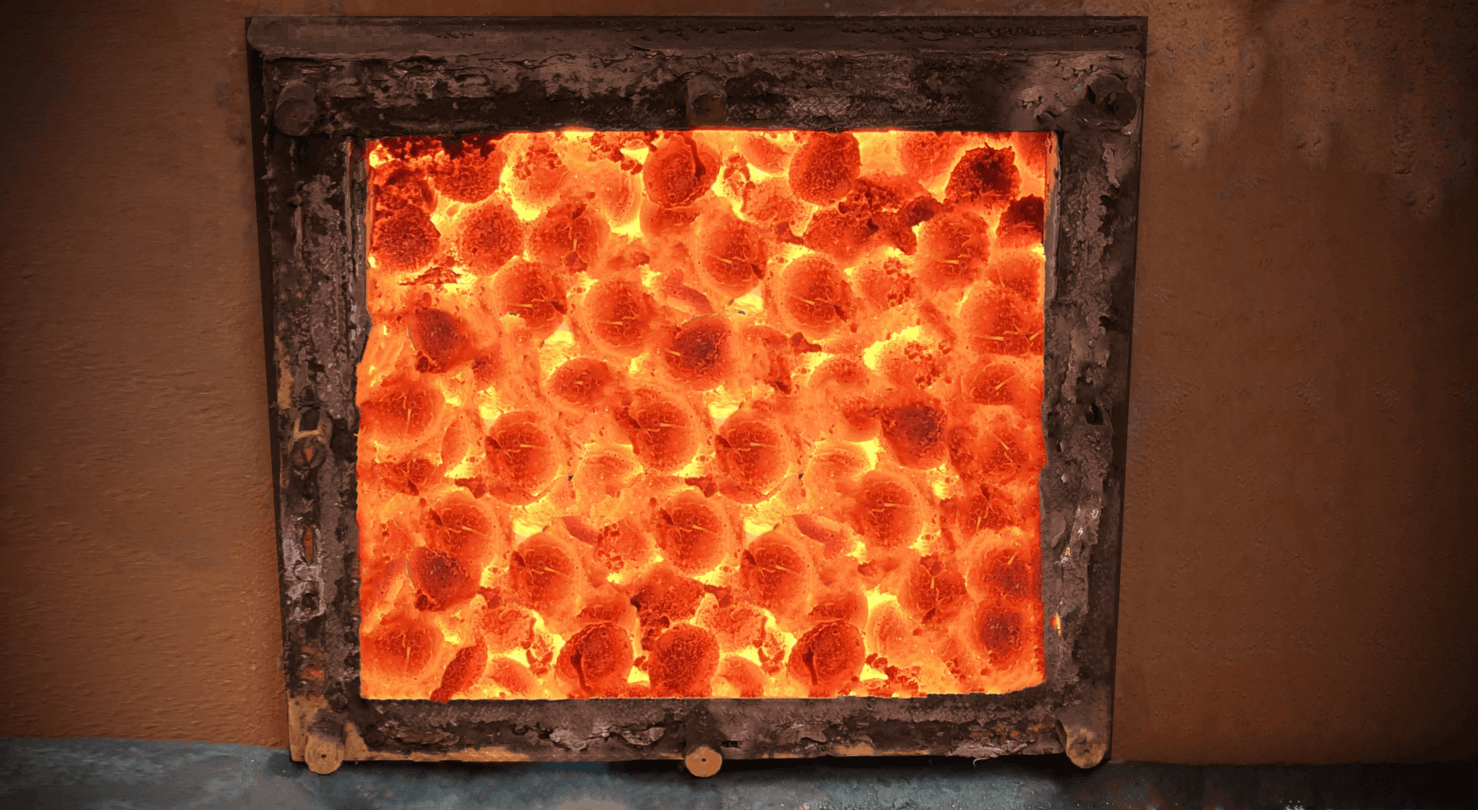
Tecnored Furnace: the solution for a radical change in pig iron production
From a metallurgical standpoint the main difference lies in reduction chemistry. Whereas the iron ore agglomerates in a blast furnace are reduced by CO gas, the iron ore in a Tecnored furnace is reduced within a “self-reducing” briquette – a briquette composed of iron oxide fines and carbon (coal or bio-char) reductant.
By combining fine particles of iron oxide and the reductant within the briquette both the surface area of the oxide in contact with reductant and, consequently, the reaction kinetics are increased dramatically. The self-reducing briquettes are designed to contain sufficient reductant to allow full reduction of the iron-bearing feed contained, together with fluxes to provide the required slag chemistry. The briquettes are cured at low temperatures prior to feeding to the furnace.
The heat required to drive the reaction within the self-reducing briquettes is provided by a bed of “Fuel” briquettes onto which the self-reducing briquettes are fed within the furnace
These “fuel” briquettes are also cold-briquetted and cured at low temperatures prior to feeding to the furnace. The material is loaded through side feeders directly in the lower shaft of the furnace.
The energy used in the process is generated in two stages:
1. by the direct burning of the fuel in the raceway (primary tuyeres) using hot air at 800ºC generating CO, CO₂ and heat
2. by the post-combustion of the CO gas with cold air injected through secondary tuyeres just below the bed of self-reducing briquettes
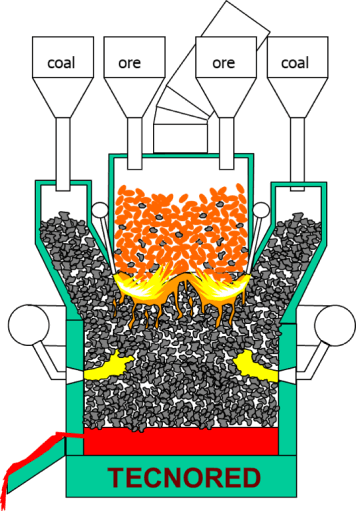
The furnace can be divided into 3 distinct zones:
